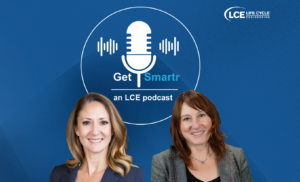
No matter how smart your equipment, it’s nothing without the people who make it work. That’s where LCEsmartr comes in. Let us help you build the smart culture needed to enable smart operations.
Automotive & Manufacturing ♦ Chemicals ♦
Consumer Packaged Goods ♦ Energy & Utilities ♦ Food & Beverage ♦ Life Sciences ♦ Oil & Gas ♦ Metals ♦ Mining ♦ Transportation
Let’s Talk
Each member of our team brings deep experience from the field and a mindset to help. And when you choose LCE, our people become your people. Your Mission. Accomplished.
Cybersecurity and IT Solutions
Integrated Logistics Support
Marine Engineering
Training and Workforce
Development
Waterfront Fleet
Maintenance
Let’s Talk
Learn about asset management, root cause analysis, planning and other reliability topics from experts who truly care about solving difficult problems, supporting people’s development, and helping you achieve the best outcomes. Register now.
Have a question?
Our learnings. Your resources. The #1 ranked section of our website. Why? It’s all the tools, resources and guides you need. Dig in.
Success only happens when we see it in others. We wake up every day to put our collective experience, skills and talents to work for the success of your operation. Learn more.
We help organizations and teams with asset-intensive operations improve operational effectiveness in private industry, public entities, government organizations and the military. Since 1976, LCE has successfully implemented engineering, asset management, reliability, maintenance and information technology solutions worldwide by combining a staff of industry experts, unique and proven processes, and comprehensive education courses. Learn more about our Solutions & Services.
We get up in the morning to use our collective skills and experience to help each other and our clients achieve their full potential.
In every aspect of our business our actions always drive people and organizations to achieve their long-term performance capability (not solely their short-term profit or cost-cutting targets).
We serve a variety of markets from private and public asset-intensive manufacturing plants and facilities to the U.S. Department of Defense, including all branches of the military and other federal agencies. To learn more about some of the challenges we help our clients solve, please visit our Customer Success section.
Let’s Talk
See yourself at LCE. We’re committed to helping you see personal success as you help your colleagues and clients achieve it, too.
Your career success. Our mission.
Let’s Talk
When your site follows reliability engineering best practices, it becomes more productive, proactive, and profitable
How much does a breakdown cost you? A recent graduate of our Reliability Engineering Certification program estimates every hour of unplanned equipment downtime costs his operation nearly $50,000.
That’s not on the high end, either – Siemens reports the cost of a lost hour now ranges from an average of $39,000 for factories producing fast moving consumer goods, to more than $2 million an hour in automotive. Among Fortune Global 500 companies, the annual cost of downtime is $129 million per facility.
The toll of unplanned downtime goes beyond financial concerns such as higher operating and maintenance costs and lower productivity. There are also human costs, like:
You may think you need a reliability engineer. What you may need is a reliability transformation. If your team is in firefighting mode, trying to get offline machines back up and running, a single person isn’t going to be enough. That’s where we come in.
We pioneered the Reliability Excellence® movement, and have been helping companies improve for almost 50 years.
Whether facilities are new or old, large or small, simple or complex, reliable operations require a shared set of values, common performance expectations, proven work processes and well-established measurement criteria. In these operations, a focus on reliability engineering becomes a competitive advantage by directly impacting cost, quality, throughput and safety.
It’s why we invented Reliability Excellence — a proven process that views an operation holistically by looking at equipment, people, processes and technology — to promote reliability throughout your organization. The Reliability Excellence journey requires building the foundation of principles and culture, establishing and optimizing the processes and procedures that
create reliability, and putting in place the management and reporting elements
that drive sustainability and continuous improvement.
The result? A collaborative relationship between maintenance and other departments, such as engineering, operations, production, quality, finance and regulatory, that’s critical to achieving and sustaining excellence and overall business performance.
With an RBAMⓇ strategy, you’ll get the most out of your physical assets while preserving their capital value, optimize your maintenance schedule for increased asset uptime, and meet production specs.
At some point, your assets are going to need maintenance to avoid breakdown. Breakdowns and equipment failures happen — it’s not a matter of if, it’s when. Reliability centered maintenance is about understanding how equipment fails and the most effective way to address the failure.
Risk-based asset management takes that a step further. We’ll help you identify your most critical assets and the risk they pose to your bottom line in the event of a major failure, then develop a strategy to cover the life cycle of your assets and improve site reliability.
At our core, LCE is focused on industrial asset management and optimization. We’ll help you reduce operating costs and improve site reliability to increase productivity and output. But it’s not enough to address your physical assets. To be effective and sustainable, your asset management strategy needs to consider people, process and technology, too.
We’ll start where you are and look at that whole picture, and what it can look like when you’re making the most of each element – what we call a ‘smart culture’. We’ll assess your current systems and identify opportunities and gaps. From there, we’ll work with you to develop the necessary processes and capabilities to create a measurable and robust asset management plan.
We’ll also help you create a culture of continuous improvement, because once you achieve Reliability Excellence, you’ll find the time your team’s been using to fight fires can be invested in making further improvement. You’ll create a loop of continuous optimization!
At our core, LCE is focused on industrial asset management and optimization. We’ll help you reduce operating costs and improve site reliability to increase productivity and output. But it’s not enough to address your physical assets. To be effective and sustainable, your asset management strategy needs to consider people, process and technology, too.
We’ll start where you are and look at that whole picture, and what it can look like when you’re making the most of each element – what we call a ‘smart culture’. We’ll assess your current systems and identify opportunities and gaps. From there, we’ll work with you to develop the necessary processes and capabilities to create a measurable and robust asset management plan.
We’ll also help you create a culture of continuous improvement, because once you achieve Reliability Excellence, you’ll find the time your team’s been using to fight fires can be invested in making further improvement. You’ll create a loop of continuous optimization!